Screw compressors consume a significant amount of energy, which has a major impact on a company’s overall energy balance. Thanks to new technologies, it is now possible to efficiently modernize existing fixed-speed compressors, resulting in cost savings and improved energy efficiency. MIKROEL solutions enable companies to achieve these benefits without the need to replace existing equipment.
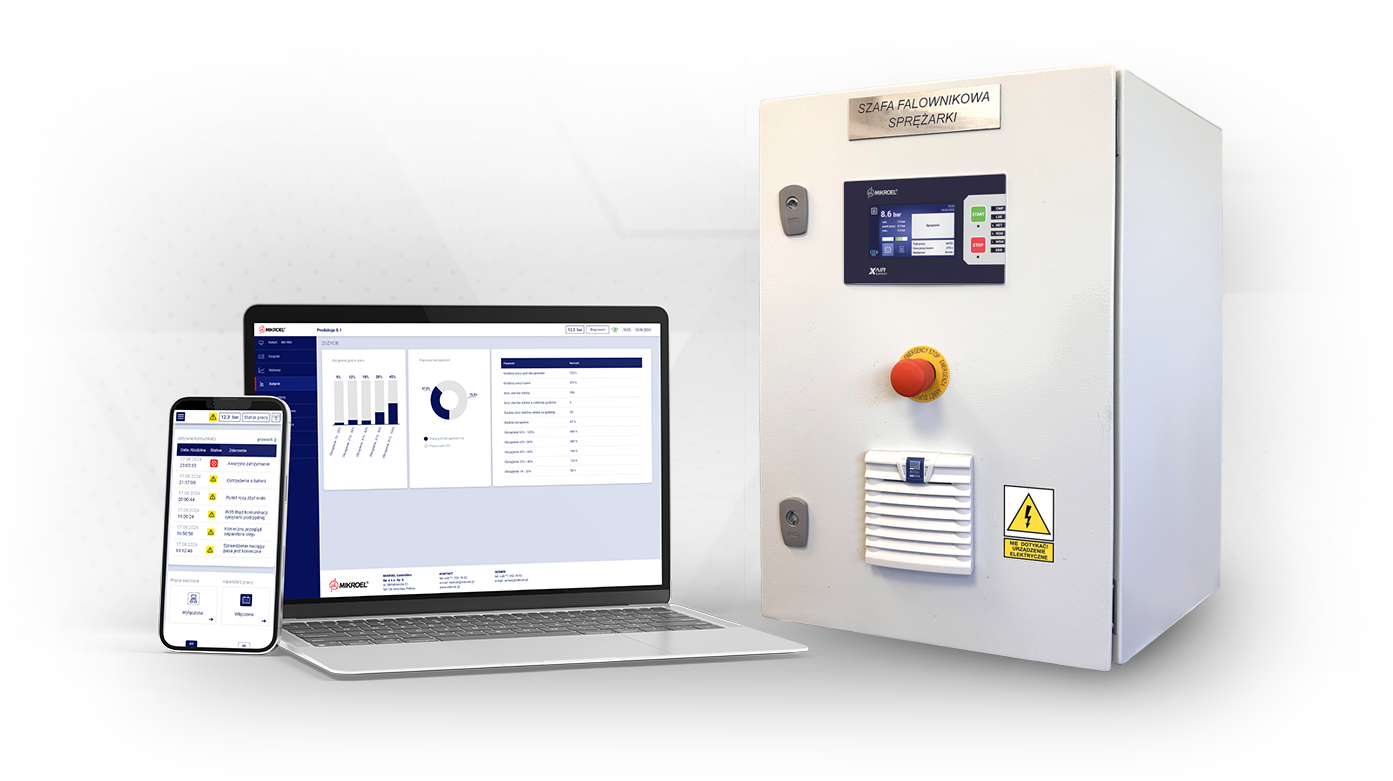
Is it worth investing in compressor modernization?
Compressed air generation is a key component of many industrial processes, accounting for 10–35% of electricity costs in manufacturing facilities. In practice, compressed air functions as the “fourth utility” alongside water, electricity, and gas, playing a vital role in production efficiency. However, traditional fixed-speed compressors can lead to high operating costs, especially when air demand varies.
Professional compressor modernization involves replacing the entire control system, which allows for reduced energy consumption and a quick return on investment, eliminating the need to purchase new machines. MIKROEL’s solutions, based on advanced control technologies, offer much more than just power savings. They enable compressor optimization, extend service life, and introduce remote visualization systems and other features that improve monitoring and allow integration with the end user’s internal systems. With MIKROEL systems, modernization not only improves energy efficiency but also enhances overall operational performance.
Modernization Profitability Analysis
Before deciding to modernize a compressor, it is essential to carefully assess whether the machine is suitable for the planned upgrade and whether it meets motor insulation requirements. To do this, a detailed audit is carried out to evaluate the feasibility of modernization. Based on data collected from compressor analyzers, key parameters are analyzed, such as power consumption, operating time under load, number of start cycles, and idle running time. The result of this process is a report that clearly determines the economic viability of the proposed modernization.
Optimization of Compressed Air Production
MIKROEL’s unique solution enables the safe execution of professional energy modernizations for screw compressors. It is based on replacing the traditional star-delta motor starting system with full-range speed control via a frequency inverter, which requires the complete replacement of the compressor’s control system. By smoothly adjusting the motor speed to match actual air demand, energy consumption can be reduced by up to 35%. An added benefit of this solution is the reduction of mechanical load on the motor, which extends the compressor’s service life.
Another advantage of compressor energy modernization is reactive power compensation. Additionally, using a frequency inverter allows for smooth startup and shutdown of the compressor motor, reducing electrical disturbances and power surges in the company’s internal power network—typically caused by large induction motors.
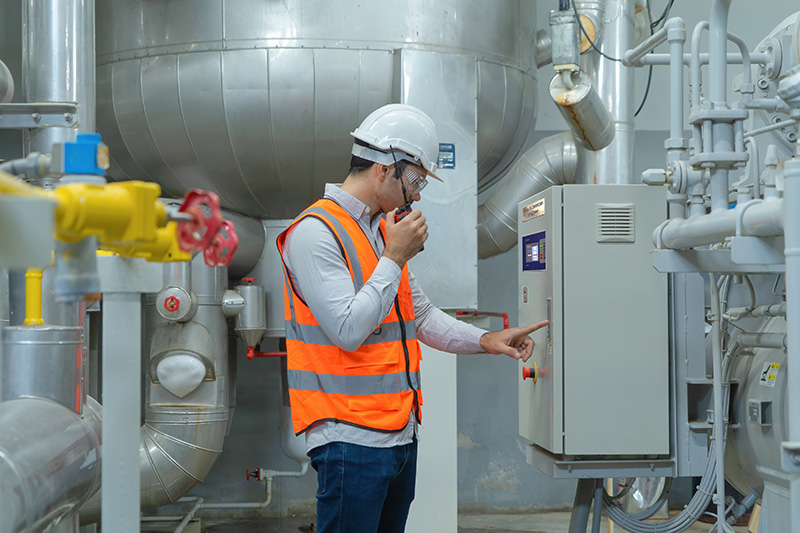
Key Components of the Modernization Package
The entire MIKROEL modernization package is housed in a compact cabinet that takes up minimal space in the compressor room. The core of the system is a control unit based on controllers from the XAIR Line, integrated with a frequency inverter and a Remote Monitoring and Diagnostics System – the Webserver. Remote data access provides full control over compressor operation, enabling performance optimization as well as real-time monitoring and diagnostics of potential issues.
One of the key advantages of the XAIR Expert controller is its exceptional ease of use. The controller displays clear and readable text messages, allowing operators to quickly understand the situation. Unlike standard inverters, which communicate errors using codes like “E01”, the XAIR Expert presents full, understandable descriptions such as “E01 Critical Error: Power Supply Asymmetry”.
A few example translations of the same error messages
Message displayed on XAIR Expert | Message on the inverter |
---|---|
oH3 Motor Overheating Warning. The AC motor drive detects excessive internal motor temperature. | oH3 |
oSPD Overspeed Warning | oSPD |
A9 Critical Error: Inverter Overload | A9 |
A12 Critical Error: Torque Limitation | A12 |
GF Ground Fault Error | GF |
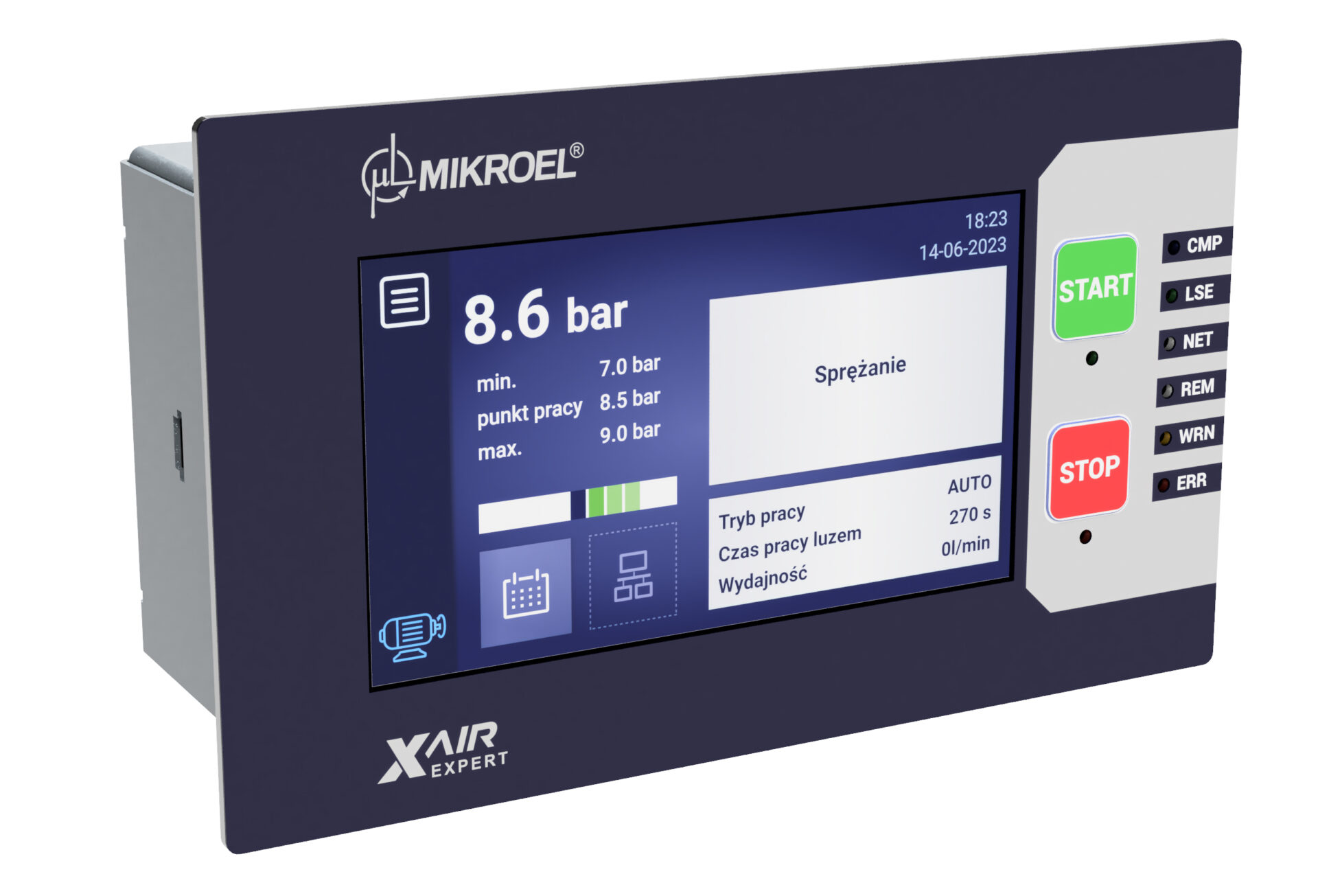
The XAIR Expert controller is designed so that the user does not need an additional inverter manual to interpret errors. All messages are displayed in a clear and user-friendly format, making operation easier and minimizing the risk of operator errors.
Remote Monitoring and Diagnostics System
A truly unique feature of the modernization package is the Webserver built into the controller (Remote Monitoring and Diagnostics System for Compressors), which enables fully visualized real-time analysis of compressor operation. Thanks to this solution, maintenance managers and compressor service teams can continuously monitor all operating parameters, analyze the settings of specific functions, such as the compressor’s operating schedule and review messages reported by the device. An additional advantage is the ability to integrate with SCADA systems and other internal systems of the end user.
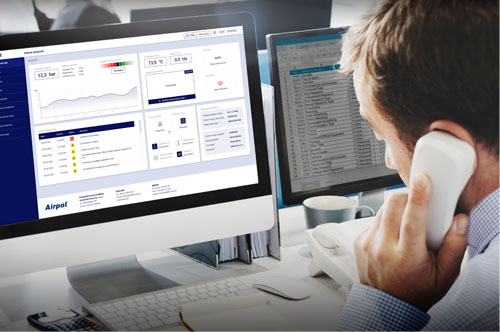
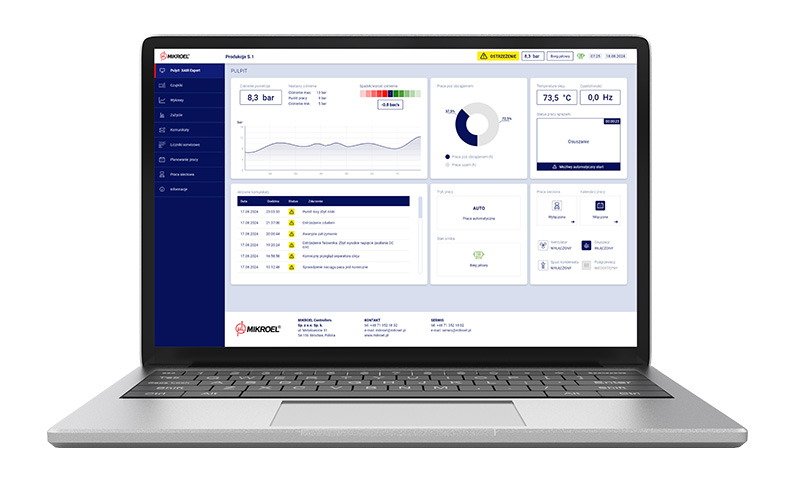
Webserver Cybersecurity
Currently, most compressor suppliers equip their devices with visualization systems based on the manufacturer’s external cloud services. These solutions depend on internet access at the facility and operate outside the company’s internal IT infrastructure, placing them beyond its control.
The controllers used in MIKROEL’s modernization kits eliminate these risks. They feature a built-in internal Webserver that stores and hosts data directly from the compressor controller. All data is processed and transmitted locally within the company’s internal LAN network. This solution ensures complete data isolation, eliminating the risks associated with using external clouds or servers. As a result, full control over data is maintained, and isolation from the public network significantly reduces the risk of cyberattacks that could disrupt production continuity.
The new controllers from the XAIR Line series feature an optional built-in Webserver system, which is hosted directly from the controller onto the internal LAN network. This provides the highest level of cybersecurity.
Remote Communication with Service Support
XAIR Line control systems are equipped with remote communication capabilities. Using an encrypted VPN channel, the company can securely transmit compressor operating parameters and status to the service team, with real-time data visible via the Webserver panel. This solution saves time and money by minimizing the number of on-site service visits. With access to the Remote Monitoring and Diagnostics System, service technicians can remotely support the operator, optimize settings, and gather additional information about the machine’s condition. If an on-site visit is required, technicians arrive already prepared with the necessary parts—eliminating repeated trips and speeding up the repair process. This approach helps minimize the risk of production downtime.
VPN technology ensures secure communication, allowing the facility to transfer data directly to the service team while maintaining full control over what information is shared. Integration with the service team requires no additional software or hardware, as the XAIR Webserver is a web-based application accessible from any browser.
White Certificates
The goal of energy modernization is to improve energy efficiency and reduce electricity consumption, which qualifies companies to obtain White Certificates. This system, regulated by the Energy Efficiency Act of May 20, 2016, allows businesses to receive financial compensation for implementing improvements that result in measurable energy savings.
White Certificates confirm the amount of energy saved and can be traded on the Polish Power Exchange (TGE) or in bilateral transactions registered on the exchange. In 2023, the substitute fee for 1 toe (tonne of oil equivalent) was 2,125 PLN, with an annual increase of 5%. Our solutions, such as the modernization or replacement of industrial equipment, may meet the conditions required to obtain these certificates, provided that the energy savings reach at least 116.3 MWh per year or 418.68 GJ per year—this can already be estimated based on the pre-implementation audit report.
Safe Implementation of Modernization
The energy modernization kits from MIKROEL Controllers are CE-certified, ensuring compliance with European safety standards. Adherence to the guidelines outlined in the Machinery Directive is confirmed through additional safety audits. An important aspect of the system is the use of internal hosting within the Compressor Remote Monitoring and Diagnostics System, as it keeps data access fully under the user’s control. To maintain the highest standards, modernizations can only be carried out by service providers authorized by MIKROEL Controllers.
Summary
The key benefits of modernization with the MIKROEL system are:
- Economic viability verification audit
- Significant reduction in electricity consumption
- Reactive power compensation and disturbance reduction
- Eligibility for obtaining White Certificates
- Extended compressor service life
- Remote Monitoring and Diagnostics System
- Data monitoring within the internal LAN network
- Remote diagnostics available to service providers
- Possibility of integration with SCADA systems