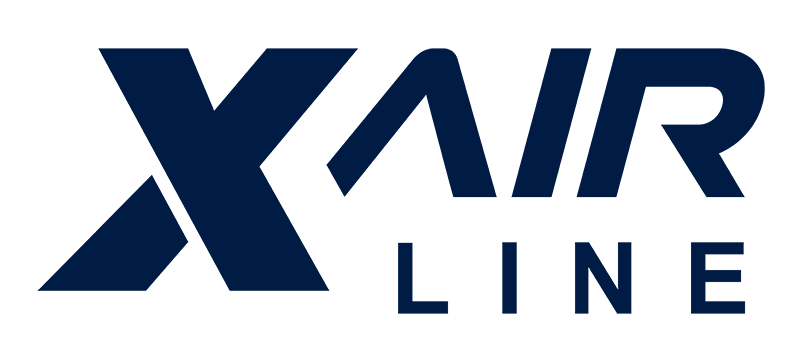
The XAIR Line platform introduces groundbreaking opportunities for service providers aiming to improve service quality and stand out in the market. Older controller models still in use offer barely half the functionality available in modern XAIR Line solutions. New features such as intuitive operation and a built-in Webserver enable remote support, opening new possibilities for customer service. Now, service providers can not only boost the efficiency of their operations but also deliver a higher level of responsiveness, support, and careadapting to the rapidly evolving demands of the industry.
Benefits delivered by the new XAIR Line series:
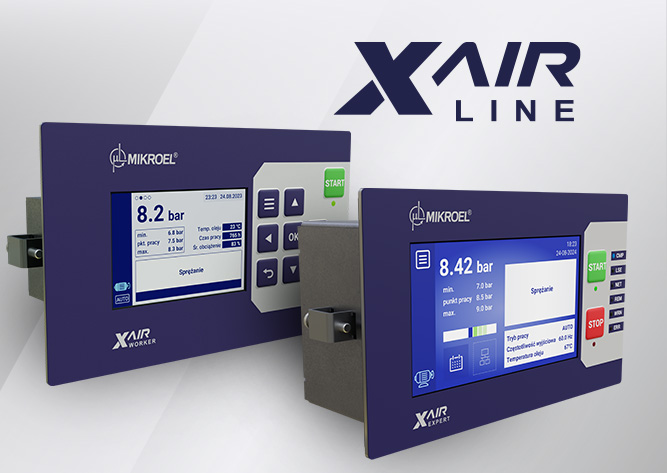
1. XAIR Line series for all compressors
The XAIR Line controller series is suitable for all oil-injected screw compressors. This means that a service technician only needs to carry one controller that can be used in any compressor. There’s no longer a need to be familiar with every controller on the market or have unique expert knowledge to replace one compressor.
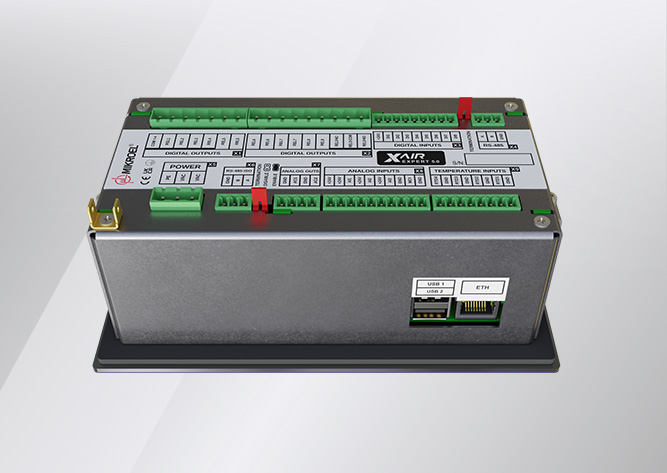
2. Full configurability of controllers
XAIR Line controllers offer flexible input and output configuration, allowing the controller to be adapted to various types of compressors. Support for many popular sensors eliminates the need to replace them you simply select the appropriate option from the device menu
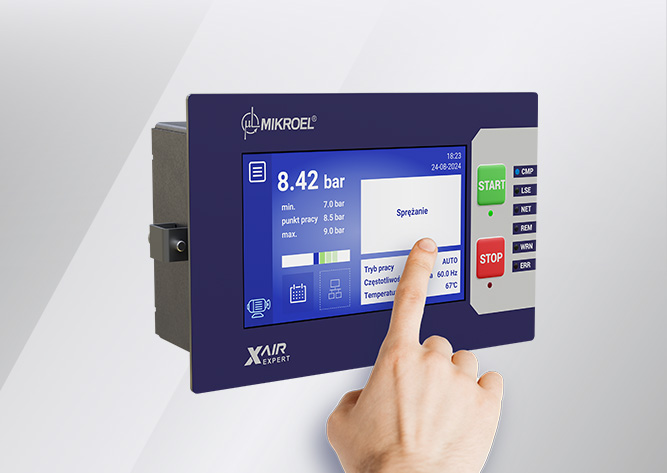
3. Intuitive control panel – just like a smartphone
Modern control systems must offer clarity and ease of use for both the customer and the service technician. That’s why XAIR Line controllers present all content in the form of descriptions, explanations, and comments, which combined with exceptional intuitiveness significantly speeds up service work.
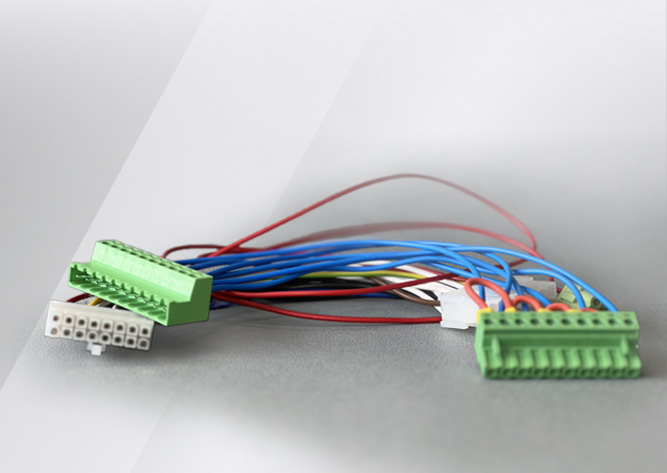
4. Dedicated wiring harnesses
In addition to full configurability of input and output equipment, the new XAIR Line product series offers optional adapter harnesses for the most commonly replaced controllers on the market. This significantly speeds up controller replacement and helps avoid mistakes when reconnecting wires.
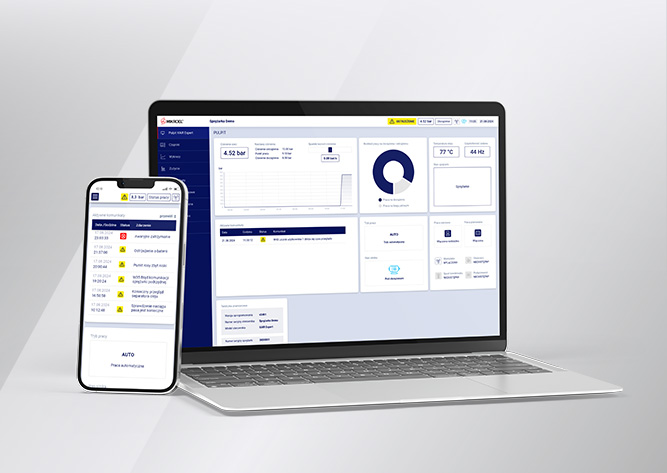
5. Remote support and compressor room monitoring
The built-in Webserver allows remote monitoring of compressor status, controlling counters, warnings, errors and other parameters, allowing for immediate technical support and precise preparation for service visits.
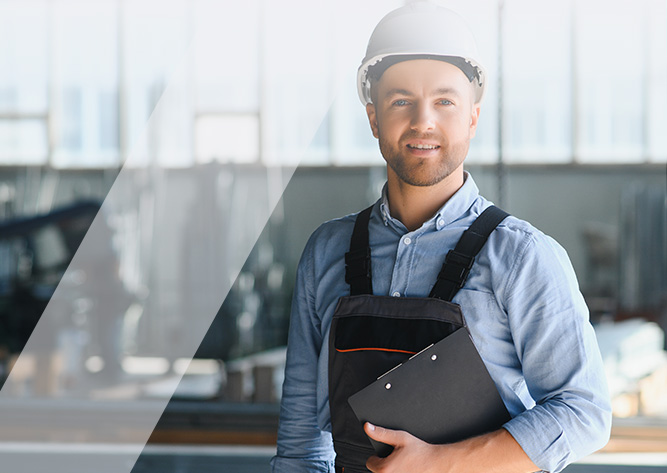
6.Precise scheduling of customer visits
With remote access to full compressor condition data, service technicians can accurately diagnose problems before they arrive, increasing efficiency and reducing the cost of service visits.
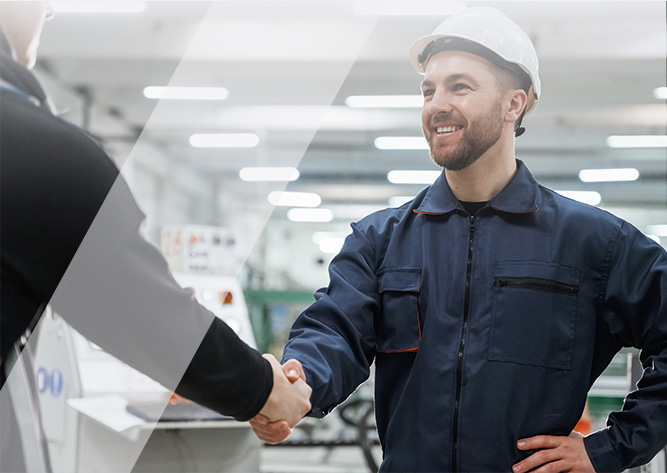
7. Building customer loyalty
High-quality service and ongoing monitoring help build customer trust and loyalty by offering fast response times and professional support even remotely.This also opens up additional opportunities for establishing service agreements.
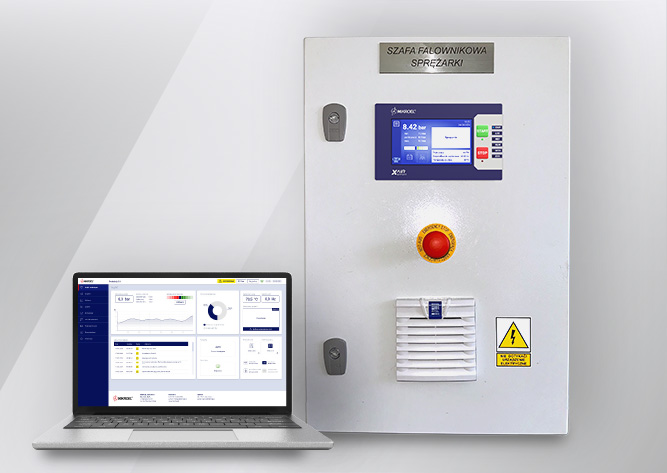
8. Modern solutions instead of outdated systems
Modern XAIR Line controllers enable fast and efficient replacement of outdated systems, providing access to the latest technologies and features, including remote compressor monitoring and integration with the customer’s internal systems, such as SCADA and MES.
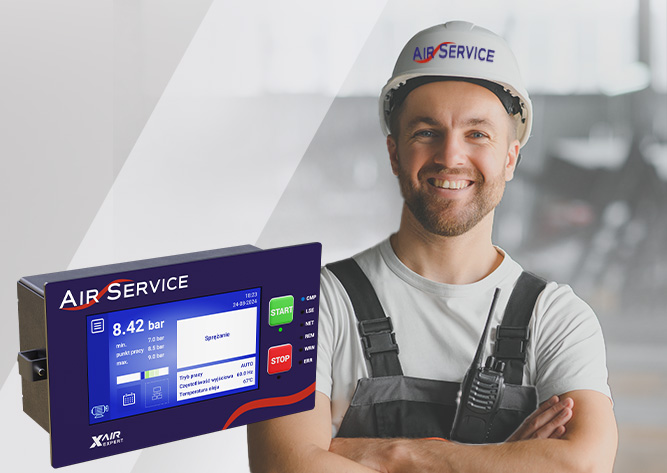
9. Differentiating your services from the competition
Using the latest technological solutions allows service providers to stand out in the market by offering top-tier services. The new XAIR Line enables strategic development of a competitive edge, aligned with Industry 4.0 trends and increasing cybersecurity requirements. What’s more, XAIR Line offers the possibility of distributing devices under your own brand, further strengthening partners’ market position.
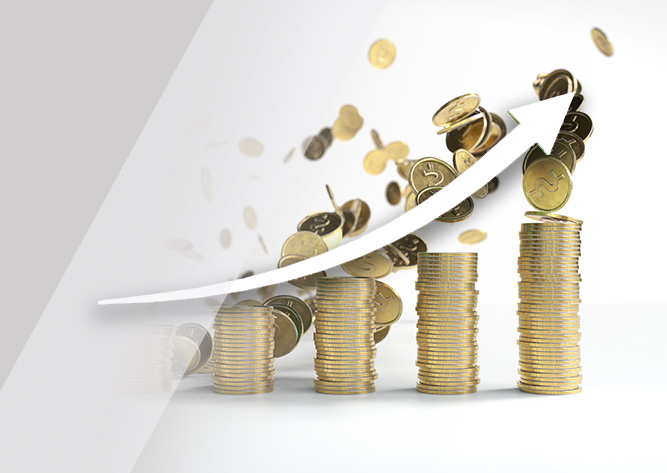
10. Cost reduction and revenue growth
XAIR Line provides tools that significantly reduce operating costs for service providers by limiting the number of site visits, improving visit planning, shortening service time, and accelerating the onboarding of new technicians. It also enables the introduction of new services related to monitoring and optimizing compressor performance.
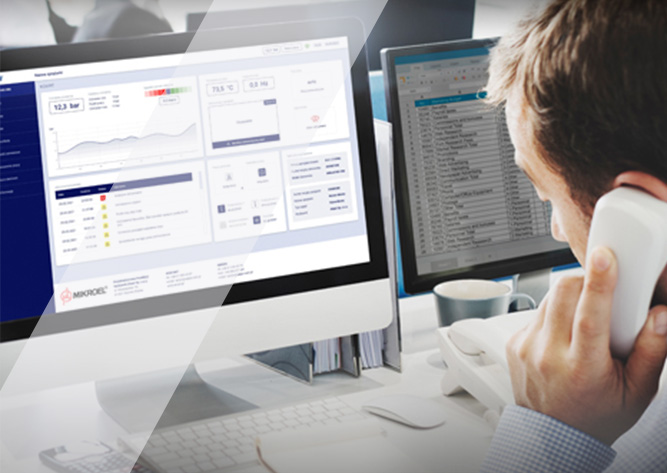
11. MIKROEL Technical Support Department
MIKROEL Controllers offers service providers professional training and ongoing technical support, which is a unique policy among manufacturers of compressor control systems. The update system in the XAIR Line series allows new features to be added to devices already installed at customer sites, making these solutions future-proof.